エラストマーとは
合成樹脂の種類
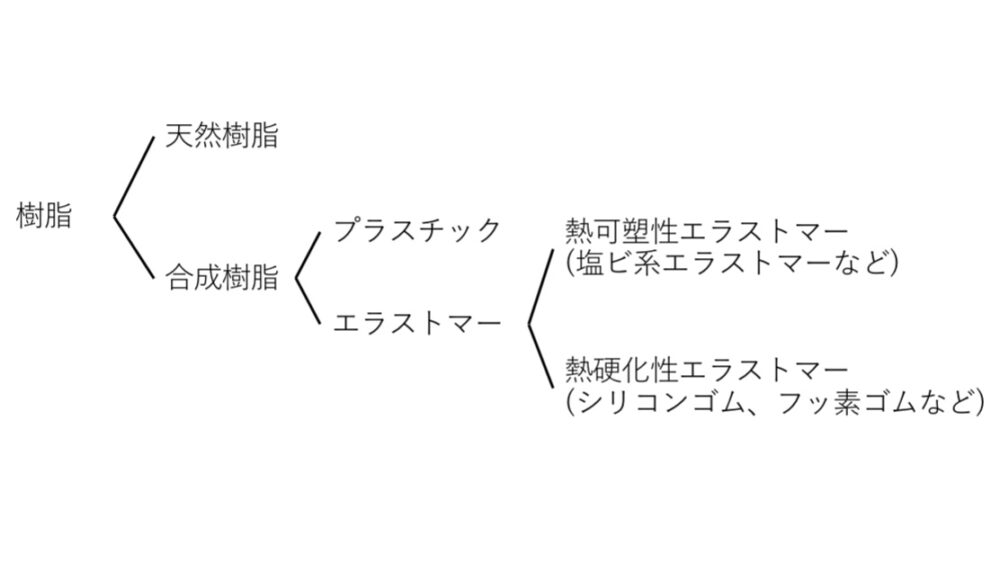
樹脂は『天然樹脂』と『合成樹脂』に大別され、樹脂製品では主に合成樹脂が使われます。
合成樹脂は更に細分化され、輪ゴムのように外力で変形してそれが取り除かれると元の形状に戻る性質(弾性)があるものは『エラストマー』、それ以外は『プラスチック』と呼ばれています。
エラストマーには、熱を加えると柔らかくなる『熱可塑性エラストマー』と熱を加えると硬くなる『熱硬化性エラストマー』があります。前者をエラストマー、後者をゴムと呼称することが多いため、本記事でもそのように呼ぶことにします。
熱可塑性エラストマーの特徴
熱可塑性エラストマー(TPE:ThermoPlastic Elastomer)は、ゴムのような弾性を持つ樹脂で、加熱すると軟化し、冷却すると再び硬化する特性があります。このため、TPEは再成形や再加工が可能で、生産後の修正や再利用ができ、コスト削減や環境負荷の低減が期待できます。
また、射出成形や押出成形など、さまざまな加工方法が使用でき、複雑な形状の部品も容易に製造できるという利点があります。しかし、加熱時に軟化しやすいため、耐熱性が熱硬化性エラストマーに比べてやや劣ることが難点です。
熱硬化性エラストマー(ゴム)の特徴
熱硬化性エラストマーは、常温では柔らかい流動的な樹脂で、加熱により化学反応を起こして硬化します。一度硬化すると再加熱しても軟化することはなく、永久的に固まった状態を保ちます。
この特性により、熱硬化性エラストマーは耐熱性が高く、高温環境での使用に適しています。しかし、再成形や再加工ができず、加工方法も限定的なため、生産後の修正が困難です。
代表的なゴムの特徴
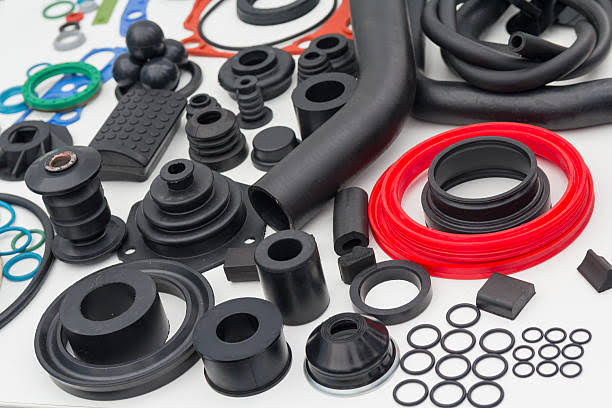
熱硬化性エラストマー(ゴム)には様々な種類があります。ここでは代表的なゴム材の特徴をご紹介します。
天然ゴム(NR)
長所:
- 機械的強度が高い
- 柔軟性と弾性が高い
- コストが安い
- 環境に良い
短所:
- 耐熱性・耐寒性が低い
- 耐候性が低い
用途:
タイヤ、ホース、ゴムベルト、シール材など、高い引張強度や耐摩耗性、弾性が求められる製品に使用されています。
シリコンゴム(Q)
長所:
- 耐熱性・耐寒性が高い
- 耐候性が高い
- 電気絶縁性が高い
- 生体適合性が良い
- 適度な弾性
短所:
- 機械的強度が低ち
- ガス透過性が高い
(透過膜など、用途によって長所になる)
用途:
電気絶縁部品をはじめ、生体適合性が求められる医療用チューブ、耐熱性や耐寒性に優れた調理器具など、様々な用途に使用されています。
フッ素ゴム(FKM)
長所:
- 耐薬品性が高い
- 耐油性が高い
- 耐熱性が高い
短所:
- 耐寒性が低い
用途:
薬品性や耐油性、耐熱性が求められる自動車の燃料システム部品や化学プラントのシール材、電磁弁やポンプの接液部などで使用されます。
ブチルゴム(IIR)
長所:
- ガス透過性が低い
(透過膜など、用途によっては短所になる) - 衝撃吸収性が高い
- 耐候性が高い
短所:
- 耐油性が低い
- 接着性が低い
用途:
ガス透過を抑える性能を活かした自動車のタイヤや薬品タンクの内張り、衝撃吸収性や防音性能が求められる防振防音材、耐候性が求められる建築用防水シートなど、幅広い用途に使用されています。
ゴムの加工方法
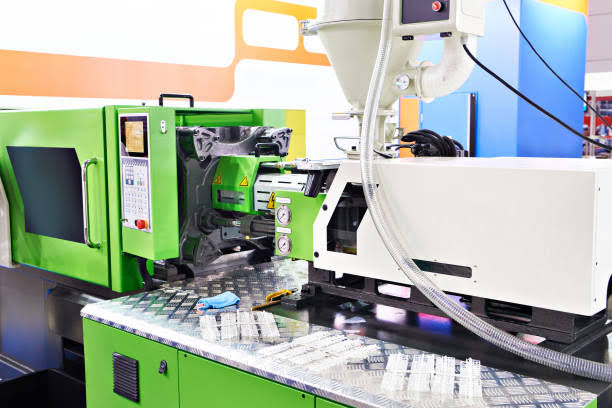
熱可塑性エラストマー(エラストマー)は常温では弾性を持つ固形の状態であり、加熱すると柔らかくなります。これにより加熱で柔らかくしてから型に流し込む射出成形や押出成形での加工が可能です。
これに対して、熱硬化性エラストマー(ゴム)は常温では流動性のある物質であり、硫黄などの添加剤を加えて加熱することで、弾性を持つ固形へと変化します。一度硬化すると元の流動体に戻ることはないため、加工方法が限定的です。
ここでは、代表的な熱硬化性エラストマー(ゴム)の加工方法をご紹介します。
- 圧縮成形:
金型に計量したゴム材を置き、熱と圧力を加えて成形します。シンプルな構造なので金型が安価です。 - 押出成形:
材料を押出口から押し出し、連続的に成形する方法です。主に熱可塑性樹脂に使われますが、粘度が高く形を維持しやすい熱硬化性樹脂(シリコンゴムなど)は押出成形が可能です。
これら2つは代表的な樹脂の成形方法です。
以下の記事で図解しているので、参考にしてください。
- トランスファー成形:
圧縮成形と射出成形を融合したような成形方法です。ゴムを適度に温めて柔らかくして金型に射出します。金型内で圧縮・加熱されて目的の形状で固まります。 - 切削加工:
硬化したゴムを旋盤やフライス盤で切削して形状を整える加工方法です。試作品の製作や少量生産に適しています。
これらの加工方法は、それぞれの特性やコスト、用途に応じて選択されます。特に切削加工は、柔軟性が必要な設計変更や試作段階で重宝されます。
弾性材料の注意点
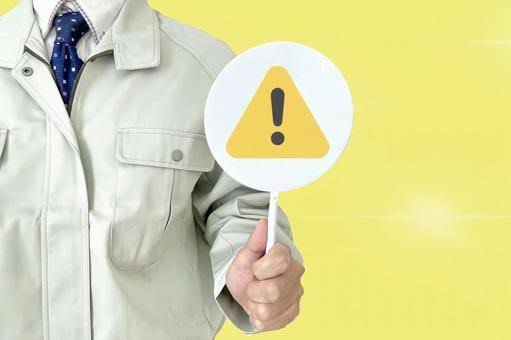
弾性材料は、その特性から加工後や使用中に寸法が変化しやすいという特徴があります。そのため、製品設計や加工においては以下の点に注意する必要があります。
使用環境による寸法変化
弾性材料は環境条件に敏感であり、次のような要因で寸法が変化することがあります。
寸法が変化するとシール性能など、設計時に意図した役割を果たせない場合があるので注意が必要です。
- 温度の影響:
高温環境では膨張し、低温環境では収縮する性質があります。特に大きな温度差がある環境では、寸法変化を考慮する必要があります。 - 湿度の影響:
吸湿性の高い材料では、湿気による膨張や収縮が起こる場合があります。 - 荷重による変形:
弾性限界以下の荷重であっても、長期間荷重がかかると、弾性材料が圧縮されたまま元に戻りにくくなることがあります。
寸法公差の設定
弾性材料の寸法公差を設定する際には、次の点を考慮する必要があります。
①環境による影響
弾性材料は温度や湿度の変化により、膨張や収縮が生じやすい特性があります。
例えば、高温環境では材料が膨張し、低温環境では収縮します。また、湿度が高いと水分を吸収して膨張するため、使用環境を想定して公差を設計することが重要です。
②用途に応じた許容範囲
弾性材料は環境による影響を受けやすく、寸法が出しづらいです。
密閉性を要するシール部品や精密な機械部品では±0.1mm以下の厳しい公差が必要になる場合がありますが、クッション材や緩衝材として使用する場合は±1mm程度の公差でも問題ないことが多いため、適切な範囲で余裕のある公差を設定することが求められます。
なお、ゴム製品の一般公差は「工業用ゴム製品寸法公差表(VDI:ドイツ技術者協会)」や「ゴム成形品の寸法公差表(ISO3302-1 Class M)」で指標が定められているのでご参照ください。
寸法測定の注意点
弾性材料の寸法測定は、特性上、通常の硬質材料とは異なる注意が必要です。適切な方法で測定を行わないと、実際の寸法を正確に把握できない場合があります。
①測定条件の統一
弾性材料は温度や湿度、力の加え方によって寸法が変化するため、測定条件を統一することが重要です。例えば20±2℃に1時間以上置いてから測定するなど、工夫が必要です。
また、測定の再現性や信頼性を担保するために、測定環境を記録しておくことも大切です。
②測定力の制御
弾性材料は環境だけでなく測定力にも注意しなくてはなりません。力を加えすぎると弾性材料が圧縮され、実際よりも小さな値が記録される可能性があります。
荷重を加えずに測定できる画像測定やレーザー測定、測定力を一定に保てるダイヤルゲージなどがゴムの測定に適しています。
おわりに
本記事では熱硬化性エラストマー(ゴム)について、その種類や特徴、代表的な素材、加工方法、設計時の注意点まで幅広く解説しました。
ゴムは弾性や加工性といった特性を活かし、さまざまな分野で使用されていますが、適切に選定し、環境や使用条件を考慮した設計を行うことが重要です。
製品設計や材料選定の参考になれば幸いです。