はじめに
ねじは、私たちの身の回りにあるあらゆる製品に使われている、非常に重要な部品です。
家電製品や自動車、建築物から精密機器に至るまで、ねじの種類や形状によって適切な締結が行われ、安全性や耐久性が確保されています。
この記事では、ねじの「頭部形状」「溝形状」「ねじ山形状」といった基本的な分類と特徴、そしてねじに施される表面処理についてわかりやすく解説します。
これから機械設計や製品開発に携わる方や、新入社員として基礎知識を身につけたい方の参考になれば幸いです。
ねじの種類と用途
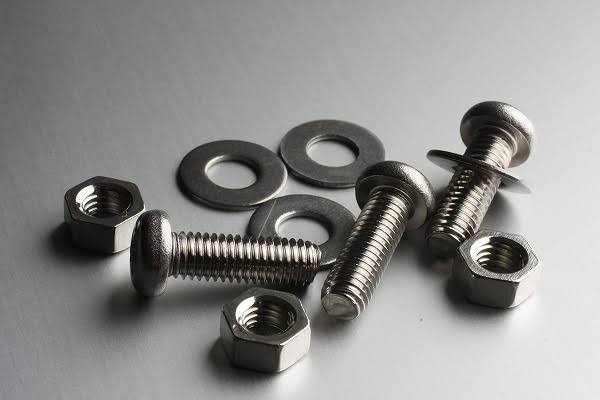
一口に「ねじ」といっても、頭の形や溝の形、ねじ山の形状によって多くの種類があります。それぞれの形状には意味があり、用途や使い方、締結方法が変わってきます。
このセクションでは、「頭部形状」「溝形状」「ねじ山形状」という3つの観点から、ねじの種類とそれぞれの用途をわかりやすく解説します。
頭部の形状(なべ頭など)
ねじの「頭部形状」は、取り付け対象や使用環境によって適切に選ぶ必要があります。
たとえば、目立たせたくない場面では皿頭、工具が入りにくい場所ではなべ頭が使われます。
代表的な頭部形状と選定のポイントを以下にまとめました。
頭部の形状 | 説明 |
---|---|
なべねじ![]() | 丸みを帯びた半球形状で、家電や電子機器の内外装など、幅広い製品に使われる最も一般的な頭部形状です。 |
バインドねじ![]() | なべねじより背が低く、径が大きいねじです。 接地面積が広いため力が分散し、相手部品が壊れにくく、緩みにくいです。狭いスペースでの締結にも適しています。 |
トラスねじ![]() | 薄い円盤形状の頭部を持ち、バインドねじより背が低く径が大きいねじです。 バインドねじの利点を強化していますが、ドライバとの噛み合わせが悪い点や、径が大きすぎてスペースを取るというデメリットがあります。 |
皿ねじ![]() | 皿のように上面が平らで、下面が円錐形状になっています。 取り付け後に頭が出っ張らないため、カバーや筐体の外側など、表面をフラットに仕上げたい場合に使用されます。 |
丸皿ねじ![]() | 皿ねじのフラット面を少し丸くしたねじです。 皿ねじより見た目が良い、引っ掛かりが少ないという特徴があり、目につきやすい外装部分に使われます。 |
六角ねじ![]() | 六角形の頭部を持ち、トルクをしっかりと伝えることができるねじです。 工具でしっかりと回すことができるため、高い締結力が求められる場所で使用されます。 |
フランジ付ねじ![]() | 頭部に円盤状のフランジを備えたねじです。 締結時に部品への圧力が均等に分散されるため、緩みにくくシール性を向上させます。ワッシャーを使う手間が省けるため、組み立て作業の効率が向上します。 |
溝の形状(プラス溝など)
ねじの頭部にある「溝」は、ドライバーなどの工具をかけて回すための重要な部分です。
プラスやマイナスのような一般的な形状から、特殊用途に使われる専用形状まで多くの種類があります。
使用目的や安全性、メンテナンス性を考慮して、適切な溝形状を選びましょう。
溝の形状 | 説明 |
---|---|
プラス溝![]() | 十字型の溝が特徴的なねじで、最も広く使用されています。 ドライバーが溝にしっかりとフィットし、締めやすさと安定性が高いため、家庭用や一般的な機械、家電製品などで頻繁に使用されます。 |
マイナス溝![]() | 1本の直線的な溝を持つシンプルな構造です。 後発のプラス溝の方が広く使われていますが、マイナス溝の方が溝内の汚れが取りやすいという特長があるため、風呂場や水回りなどでは、マイナス溝が使用されることが多いです。 |
六角溝![]() | 六角形の溝を持つねじです。 六角形の形状により高いトルクを伝達できるため、大きな締結力を必要とする場面で使用されます。主に機械部品や自動車、重機などの高負荷の環境で多く使われます。 |
特殊溝![]() | プラス溝、マイナス溝、六角溝以外の特殊な溝形状を持つねじです。 ヘクスローブ溝やトライウィング溝など、様々な種類があります。一般的な溝形状ではないため、ユーザーに勝手に外してほしくない箇所で使用されます。 |
ねじ山の形状(並目など)
ねじの軸部分にある「ねじ山」は、相手部品とのかみ合わせに関わる重要な要素です。
ねじ山のピッチや形状によって、ゆるみにくさ、締結力、加工対象への適合性が変わります。
使用する材質や用途に応じて、適切なねじ山を選ぶことが大切です。
ねじ山の形状 | 説明 |
---|---|
並目ねじ | 標準的なねじ山ピッチを持つねじです。多くの機械や構造物に広く使われており、部品同士の汎用性にも優れています。 |
細目ねじ | 並目ねじよりもねじ山のピッチが細かいねじです。ゆるみにくく、強度が必要な箇所や微調整が求められる場面に適しています。 |
タッピンねじ | ナットや雌ねじがない材料に対して、自らねじ山を切りながら締結できるねじです。主に樹脂部品や薄板などへの取り付けに用いられます。 |
金属ねじの表面処理
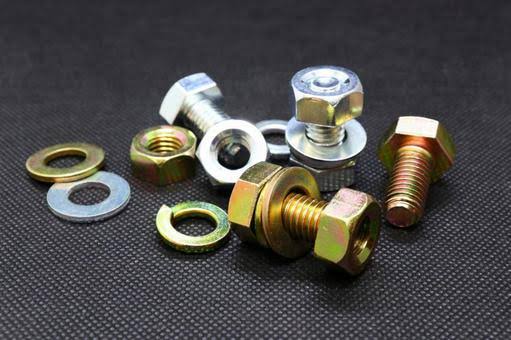
市販されているねじの多くには、防錆性や潤滑性、装飾性を高めるための表面処理が施されています。なかでも最も一般的なのが、ねじに金属皮膜を形成するめっき処理です。
表面処理の種類は多岐にわたりますが、本記事ではねじによく使われる代表的な処理方法をピックアップしてご紹介します。
亜鉛めっき
亜鉛めっきは、ねじの表面に亜鉛の層を形成して防錆性を高める処理です。
亜鉛層の形成方法には、高温で溶かした亜鉛にねじを浸す「溶融亜鉛めっき」と、電気の力で亜鉛の薄膜を均一に付ける「電気亜鉛めっき」があります。
亜鉛は、ねじ本体より先に腐食する「犠牲防食」により腐食を防ぐため、亜鉛自体の腐食は避けられません。
特に電気亜鉛めっきは膜厚が薄いため、クロメート処理など、後述する追加の処理を施すのが一般的です。
クロメート処理
クロメート処理は、クロム化合物を含む処理液にねじを浸し、化学反応によって表面にクロメート皮膜(またはクロム化成皮膜)を形成する処理です。
この皮膜は、ねじ本体や亜鉛めっき層を外部の水分・酸素・腐食因子(塩分など)から物理的に遮断する「バリア防食」により、腐食を防ぎます。
クロメート処理に使用されるクロムには、酸化数(電子を失った数=正電荷の数)の違いにより、「六価クロム」と「三価クロム」の2種類があります。それぞれを用いた処理は、「六価クロメート(または単にクロメート)」、「三価クロメート」と呼ばれます。
六価クロムは、傷がついても周囲の水分や酸素と反応して皮膜を再形成する自己修復作用があり、防錆性に優れます。
ただし、酸化力が強く、人体や環境への毒性があるため、EU(欧州連合)のRoHS指令などにより使用が制限されており、現在は安全性の高い三価クロムが主流になり始めています。
また、クロメート処理には使用する薬品や条件によって様々な色調があります。
<六価クロメートの種類>
- 光沢クロメート(ユニクロ)
- 有色クロメート
- 黒色クロメート
- 緑色クロメート
<三価クロメート>
- 白色クロメート(三価ホワイト)
- 黒色クロメート(三価ブラック)
クロムめっき
クロムめっきは、ねじ表面にクロムの皮膜を形成する表面処理です。
前述したクロメート処理と名称は似ていますが、両者は全く異なる処理です。
クロメート処理は「ねじ表面にクロム化合物を反応させて皮膜を形成する化成処理」であるのに対し、
クロムめっきは「クロムそのものを金属皮膜として付ける処理」です。
また、目的にも違いがあります。
クロメート処理が防錆性を目的としているのに対し、クロムめっきは硬度や摩耗に対する耐久性、そして美観を目的として施されます。
なお、クロムめっきはねじへの適用は比較的少なく、装飾性や耐摩耗性が求められる特殊な用途で使用されます。
ニッケルめっき
ニッケルめっきは、ねじ表面にニッケルの金属皮膜を形成する表面処理です。
ニッケルは鉄よりも腐食に強いため、外部の水分・酸素・腐食因子(塩分など)から物理的に遮断する「バリア防食」により、ねじ本体の腐食を防ぎます。
ただし、亜鉛めっきのような「犠牲防食」ではなく、皮膜に傷がつくとその部分から腐食が進行してしまうという欠点があります。
このため、「ニッケルめっき(バリア防食)」よりも、「亜鉛めっき(犠牲防食)+クロメート処理(バリア防食・自己修復)」の方が実用面で優れており、より広く使用されています。
ニッケルめっきは、主に装飾性や硬度などが求められる場面に限定して使用されることが一般的です。
黒染め(四三酸化鉄皮膜処理)
黒染めは、ねじ表面に四三酸化鉄皮膜(黒錆)を形成する表面処理です。
鉄素材をアルカリ性の処理液に浸し、高温で化学反応を起こすことで、黒色の酸化皮膜が形成されます。
この皮膜は非常に薄く、処理温度も比較的低いため、寸法変化がほとんどなく、精密部品にも適しています。また、表面が落ち着いた黒色になるため、意匠性を重視する用途にも広く利用されています。
ただし、四三酸化鉄皮膜は多孔質であり、水分が侵入しやすく、そのため防錆性が低いという欠点があります。
一般的には、防錆油などを塗布して多孔部を塞ぐ後処理が施されますが、亜鉛めっきやニッケルめっきと比較すると、防錆性は劣ります。
おわりに
ねじは一見すると小さな部品ですが、その形状や種類を正しく理解し、用途に応じて選定することは、製品の性能や安全性を確保する上で非常に重要です。
今回ご紹介した頭部形状・溝形状・ねじ山形状の違い、代表的な表面処理の種類を知っておくことで、設計や現場での対応力が大きく向上します。
今後、実際に製品の設計や組み立てに携わる際には、ぜひこの記事の内容を思い出し、最適なねじを選んでみてください。