樹脂成形とは何か
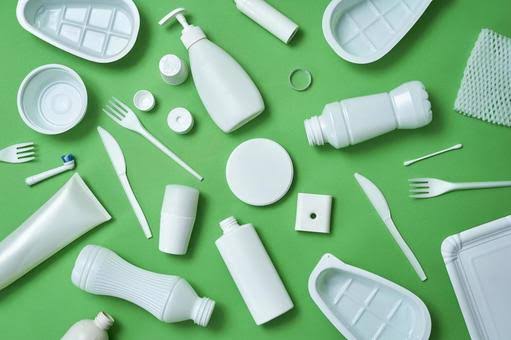
樹脂成形は、樹脂材料を使用して部品を作る製造方法です。樹脂を加熱して液体状にし、金型に射出して冷却固化させることにより、所望の形状を作ります。
樹脂成形は低コスト・高効率・優れた製品精度という特性から、自動車部品や家電製品、日用品など幅広い産業で利用されています。
しかし、成形工程は多くの変数を含む複雑なものであり、設計の不備や工程条件の不適切な管理によって様々な成形不良が発生する可能性があります。
これらの不良は製品の品質に直接的な影響を与え、製造コストの増加や生産遅延を引き起こすことがあります。
次のセクションでは、これらの一般的な成形不良の種類とその原因、対策について詳しく解説します。
主要な成形不良の種類と特徴
バリ
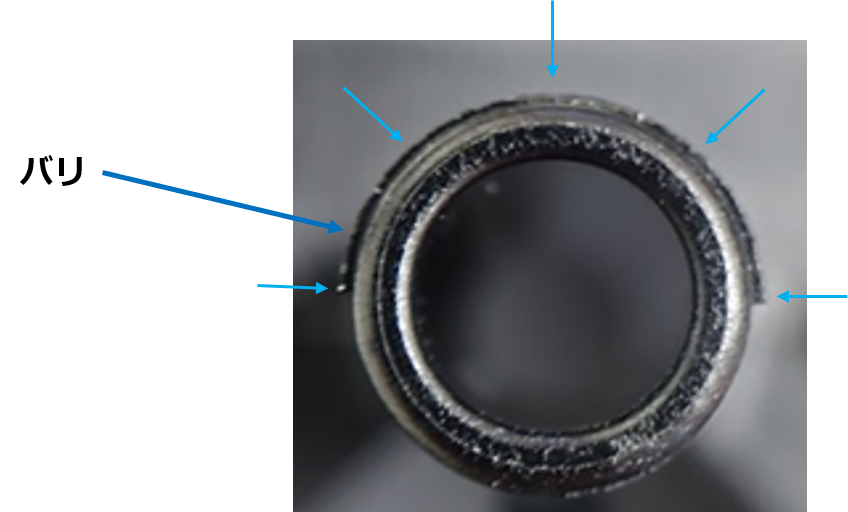
事象:
製品の外周やエッジに現れる、余分な樹脂の出っ張り。
直接原因:
成形時に金型の合わせ面(PL部)の隙間に樹脂がはみ出し、その状態で樹脂が固まる。
根本原因(候補):
- 金型のクランプ力が不足しているため、合わせ面が十分に閉じていない:クランプ力の調整や金型設計の見直しが必要。
- 金型の摩耗や損傷が原因で隙間が発生する:定期的な金型メンテナンスや必要に応じた修理・交換を行う。
ウエルドライン
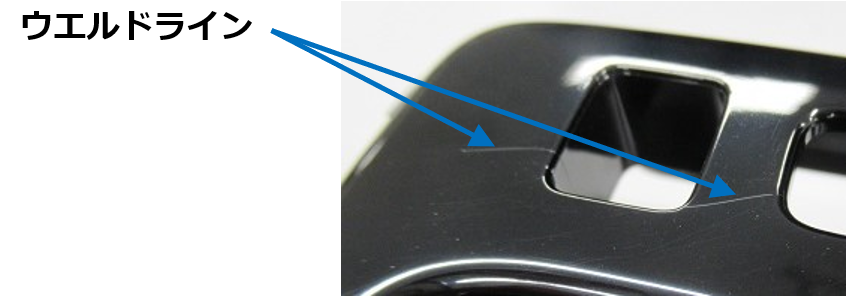
事象:
製品の表面に現れる線状の跡。薄肉部に発生しやすい。
直接原因:
金型内を流れる樹脂が分岐したのち再び合流する際、樹脂が十分に融合する前に冷えて固化する。
根本原因(候補):
- 樹脂の粘度が高い:材料の再選定。
- 樹脂の加熱時間や射出時間、速度などの成形条件が適切でない:成形パラメータを見直す。
- 金型のガス抜きが悪く、空気の逃げ場がなくなり、樹脂の充填を妨げる:ガス抜き路の改善や金型の再設計を検討。
- 薄肉など、樹脂が流れづらい製品形状である:製品設計の見直しや、流動促進措置の検討。
ショート(不完全な充填)
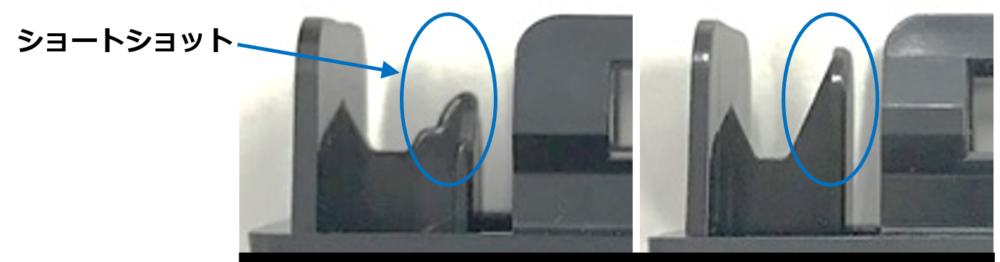
事象:
製品の表面や断面に現れる樹脂の未充填による穴。薄肉部に発生しやすい。
直接原因:
成形時に樹脂が金型全体に充填しきる前に冷えて固化する。
根本原因(候補):
- 樹脂の粘度が高い:材料の再選定。
- 樹脂の加熱時間や射出時間、速度などの成形条件が適切でない:成形パラメータを見直す。
- 金型のガス抜きが悪く、空気の逃げ場がなくなり、樹脂の充填を妨げる:ガス抜き路の改善や金型の再設計を検討。
- 薄肉など、樹脂が流れづらい製品形状である:製品設計の見直しや、流動促進措置の検討。
ボイド
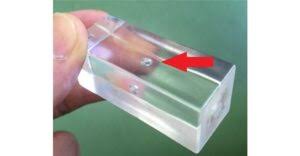
事象:
製品の厚肉部に現れる気泡。厚肉部に発生しやすい。
直接原因:
- 金型内のガスが抜け切っていない。
- 製品表面と中心部の冷却速度の差が大きく、冷却による収縮で中心部の樹脂に表面側に引っ張られる(陰圧がかかる)ことで気泡が形成される。
直接原因1の根本原因(候補):
- 金型のガス抜きが悪く、空気の逃げ場がない:ガス抜き路の改善や金型の再設計を検討。
直接原因2の根本原因(候補):
- 厚肉な製品形状である:製品設計の見直し。
- 金型温度が高すぎて、冷却による収縮量が大きい:金型温度や冷却速度など、成形パラメータを見直す。
- 充填した樹脂の量が少なく、冷却による収縮分をカバーできていない:金型の保圧力を上げて樹脂を多く流す。
シルバーストリーク(銀条)
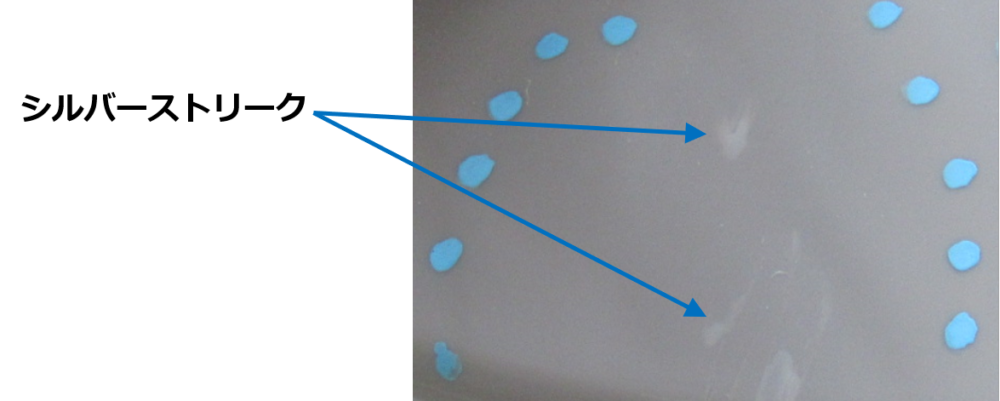
事象:
製品表面に現れる銀色のスジ模様。
直接原因:
樹脂の内部に発生したガスが、金型内で引き伸ばされてスジ模様として現れる。
根本原因(候補):
- 金型のガス抜きが悪く、空気の逃げ場がない:ガス抜き路の改善や金型の再設計を検討。
- 厚肉な製品形状である:製品設計の見直し。
- 金型温度が高すぎて、冷却による収縮量が大きい:金型温度や冷却速度など、成形パラメータを見直す。
- 射出速度が適切ではない:射出速度など、成形パラメータを見直す。
- 充填した樹脂の量が少なく、冷却による収縮分をカバーできていない:金型の保圧力を上げて樹脂を多く流す。
反り
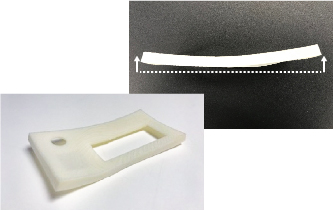
事象:
製品の表面が平らでなく反る(曲がる)。肉厚が変わる箇所に発生しやすい。
直接原因:
冷却時に製品が不均一に冷却され、部分的に内部応力が残り、反りが発生する。
根本原因(候補):
- 製品の肉厚が不均一でエリアにより冷却速度が異なる:製品設計の見直し。
- 樹脂の成形収縮率が大きい:材料の再選定。
- 金型温度が不均一(キャビティ側とコア側で温度が違う、または一部エリアの温度が違うなど):金型の温度制御の見直し。
シンクマーク(ヒケ)
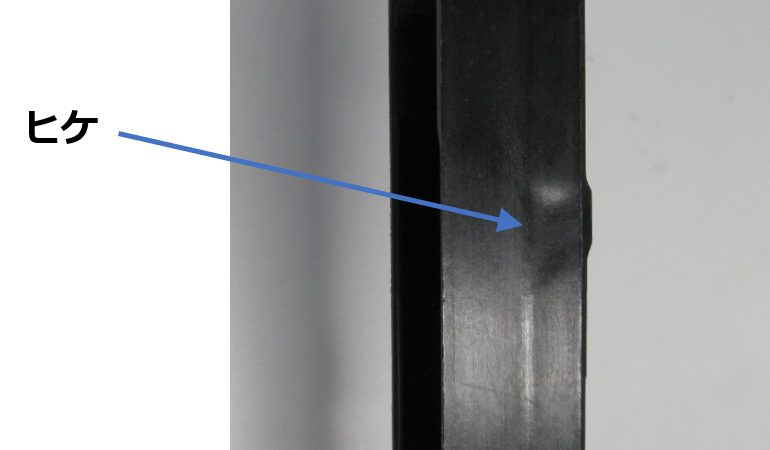
事象:
製品表面に現れる凹みやくぼみ。厚肉部に発生しやすい。
直接原因:
冷却時、製品の表面は速く固化し、内部が遅れて固化すると、樹脂の収縮により表面に凹みやくぼみが発生する。
根本原因(候補):
- 厚肉な製品形状である:製品設計の見直し。
- 樹脂の成形収縮率が大きい:材料の再選定。
- 金型温度が高すぎて、冷却による収縮量が大きい:金型温度や冷却速度など、成形パラメータを見直す。
ジェッティング
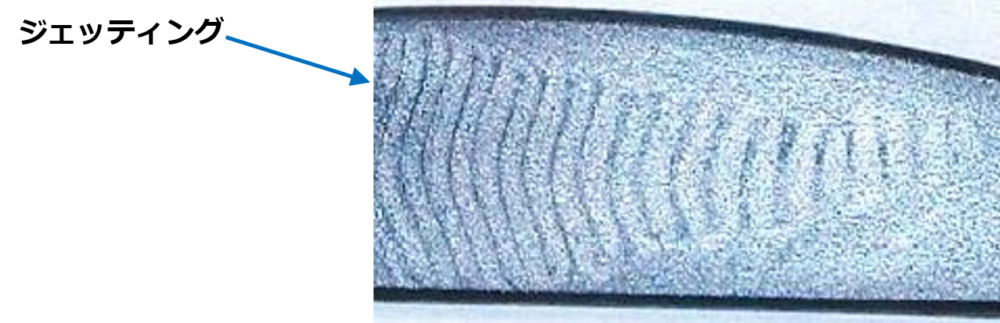
事象:
製品表面に発生する蛇が這ったような跡。ゲート付近に発生する。
直接原因:
樹脂が金型内に勢いよく射出され、その樹脂が融合が不十分のまま冷却されて固化する。
根本原因(候補):
- 樹脂の射出速度などの成形条件が適切でない:成形パラメータを見直す。
- ゲートが小さい:ゲートの再設計を検討。
フローマーク
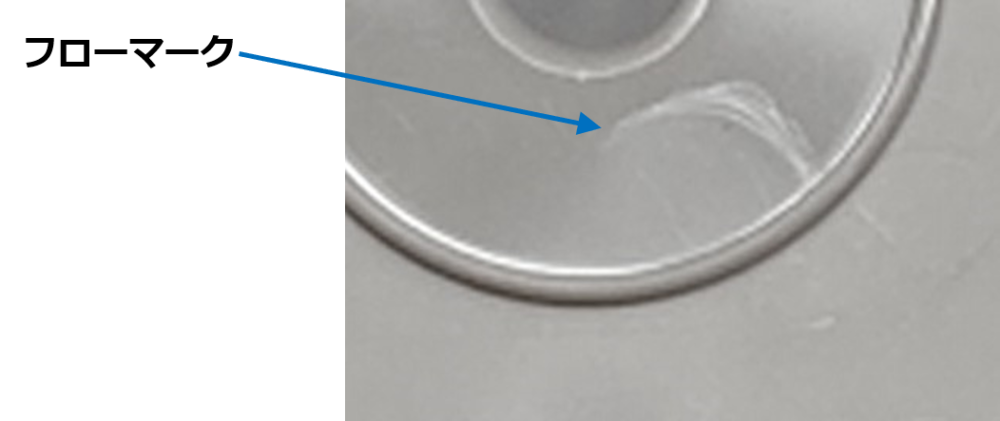
事象:
製品表面にに発生する波紋や湯じわのような跡。ゲート付近や最遠部、肉厚が変わる箇所に発生しやすい。
直接原因:
樹脂の流れが不均一であり、金型に触れた部分から冷却が始まり、樹脂の流動が局所的に妨げられることで波紋や湯じわが形成される。
根本原因(候補):
- 樹脂の射出速度や金型温度などの成形条件が適切でない:成形パラメータを見直す。
- ゲートが小さい:ゲートの再設計を検討。
- 肉厚の変化が大きい箇所がある製品形状である:製品設計の見直し。
- 樹脂の粘度が高い:材料の再選定。
焼け
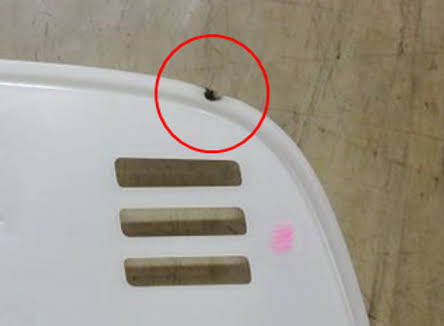
事象:
製品表面が黒色や茶色に変色し、時には焦げた臭いがする。
直接原因:
樹脂が過剰に加熱されて変色する。
根本原因(候補):
- 樹脂から発生するガスが滞留・圧縮されて高温になる:ガス抜き路の改善や金型の再設計を検討。
- 成形温度が高すぎる、または加熱時間が長すぎる:成形パラメータを見直す。
おわりに
本記事では、樹脂成形における一般的な成形不良の種類とその原因、対策について説明しました。
これらの知識が、製品の品質や生産効率の向上に活かされれば幸いです。