射出成形とは?【初心者向けに簡単解説】
射出成形の基本的な仕組み
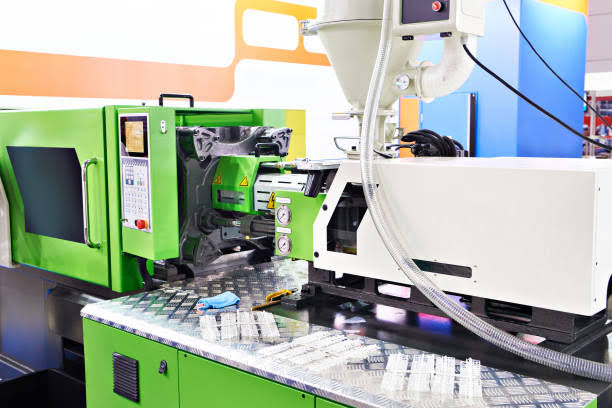
射出成形(インジェクション成形)は、熱可塑性樹脂を用いた最も一般的な成形方法です。
加熱によって樹脂を溶かし、金型に高圧で射出し、冷却・固化させることで、製品の形状を作り出します。
この方法は、薄肉・複雑形状・微細加工品なども高精度かつ高速で量産できるのが大きな特長です。そのため、自動車部品・家電・日用品・医療機器など、幅広い分野で使用されています。
射出成形は、金型設計やゲート設計が成形品の品質に大きく影響するため、設計上の理解も重要です。
なお、樹脂の成形方法には、射出成形のほかにも押出成形・ブロー成形・圧縮成形などがあります。以下の記事でそれぞれの特徴を詳しく解説していますので、あわせてご覧ください。
スプルー・ランナー・ゲートとは?
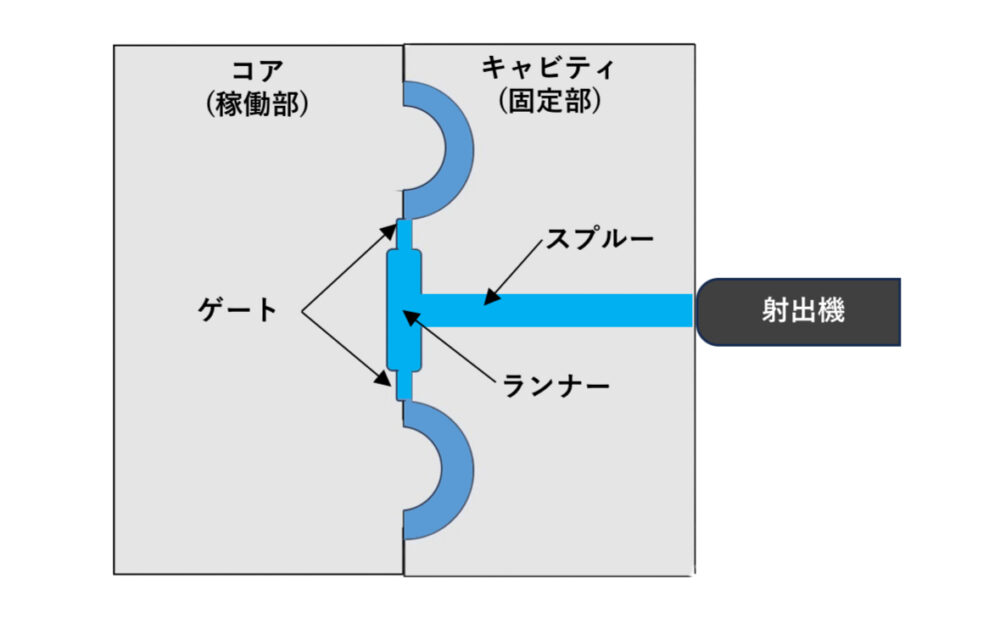
射出成形では、溶かした樹脂を金型内に射出することで、目的の形状を成形します。
このとき、樹脂が流れるルートは「スプルー → ランナー → ゲート → キャビティ(製品形状部)」という順序で構成されています。
- スプルー
スプルーは、成形機のノズルから射出された樹脂が最初に通る垂直な流路です。通常は円筒形状で、ランナーへ樹脂を送り込む役割を担います。 - ランナー
ランナーは、スプルーを流れてきた樹脂を単一または複数のキャビティ(製品形状を形成する金型の空洞部)へ分配する流路です。ランナーの形状や配置は樹脂の均一な流れや圧力損失の最小化、成形品の一貫した品質確保のために重要です。 - ゲート
ゲートは、キャビティへの入口です。ゲートは樹脂の流れる速度が重要であり、速すぎるとジェッティング、遅すぎるとフローマークという成形不良の原因になります。
このように、スプルー・ランナー・ゲートは、それぞれが樹脂の流れを適切に導くための重要な構成要素です。
次は、このうちの「ゲート」に焦点を当てて、その種類や特徴を詳しく見ていきましょう。
ゲートが品質に与える影響
射出成形プロセスにおける「ゲート」は、溶融した樹脂を金型内部へ送り込む生命線とも言える存在です。
適切なゲート設計がなければ、成形品の肉厚むらや内部応力の偏りが生じて品質不良を招き、トリミング工程の手間やコストが大幅に増加します。
ゲート位置や形状が適切でない場合、製品内に樹脂の流れムラが生じ、以下のような成形不良を誘発します。
- ジェッティング
樹脂が金型内に勢いよく射出されることでゲート付近に生じる、蛇が這ったような跡。 - ショートショット
ゲート設計が不適切で樹脂が末端まで届かず、製品の一部が未充填となる。 - ウェルドライン
金型内を流れる樹脂が分岐したのち、再び合流する箇所に発生する線状の跡。
ただし、これらの成形不良はゲート起因とは限らず、製品の形状や金型のガス抜き性など、様々な要因に起因します。
また、上記以外にも様々な成形不良があります。成形不良をもっと詳しく知りたい方は以下の記事が参考になると思います。
射出成形ゲートの主な種類と特徴
サイドゲート
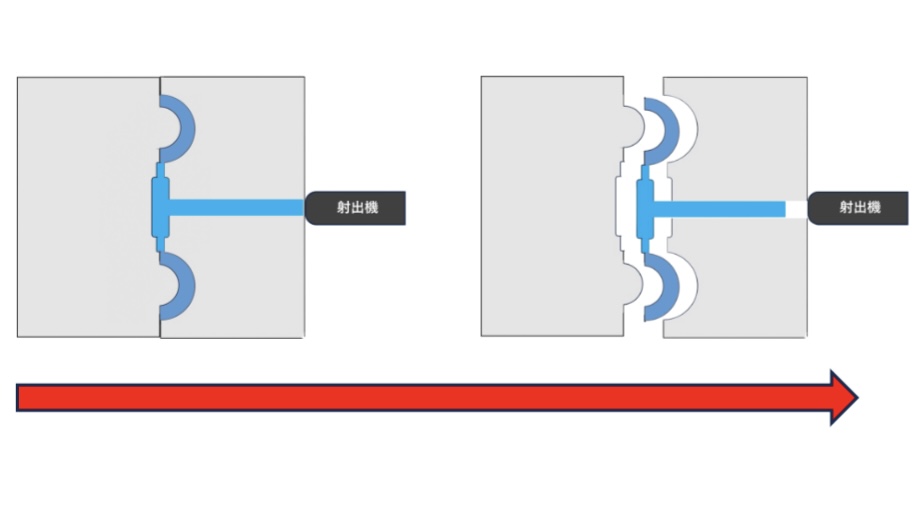
サイドゲートは成形品の側面に設置されるゲートで、射出成形で最も一般的に使用されるタイプです。
このゲートは、設計が比較的簡単で、複数のキャビティに対して樹脂を均等に分配しやすいため、大量生産に適しています。
ただし、成形品はゲート(およびランナー、スプルー)が付いた状態で取り出されるため、ゲート部分をカットする後加工が必要です。このため、ゲート跡が成形品に残りやすく、外観が重要な製品には適していない場合があります。
ピンゲート
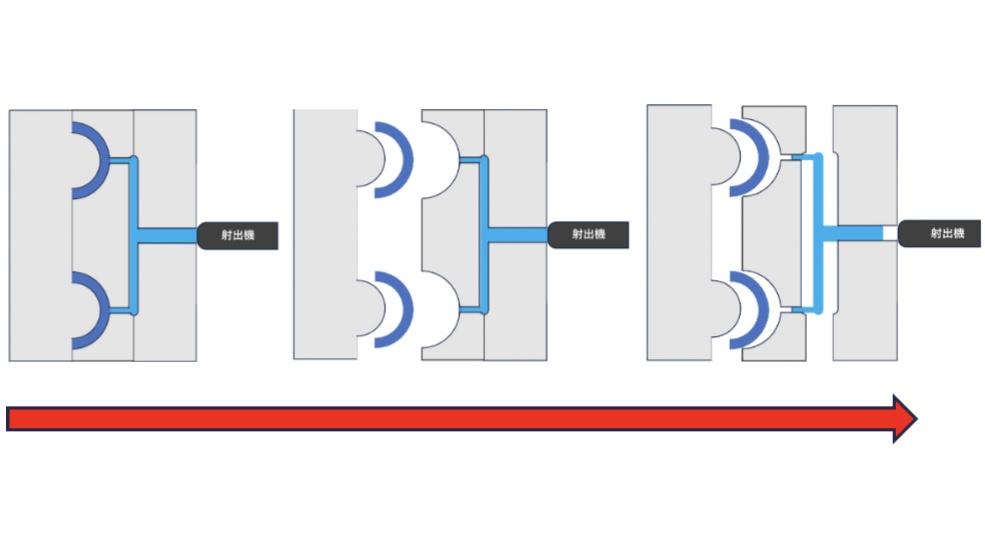
ピンゲートは、成形品の正面から樹脂を流すゲートです。
ゲートサイズは非常に狭く、円形で、樹脂をキャビティへ高速で流入させることが可能です。面の広い部品を成形する際には、複数のゲートを設けることもあります。
ピンゲートはスリープレート構造の金型で使用され、型開き時に自動的にゲートがカットされます。これは大きな利点の一つです。
ただし、ゲートサイズが小さいため、高粘度の樹脂の流れが悪くなりがちです。また、成形品の正面に位置することから、ゲート跡が目立つのもデメリットです。
トンネル(サブマリン)ゲート
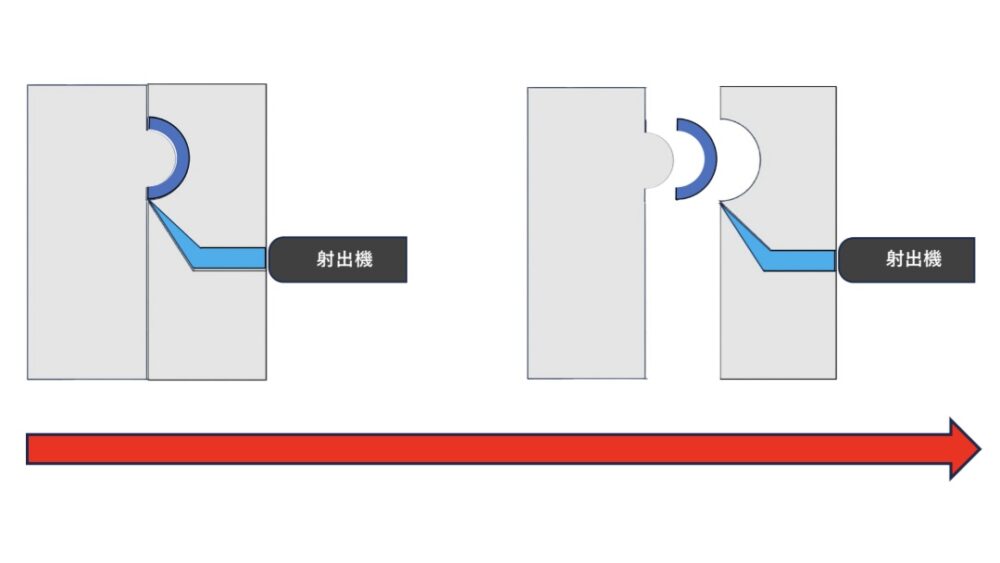
トンネルゲート(サブマリンゲート)は、ランナーから成形品に向かって斜めに繋がるゲートです。
トンネルゲートは、成形品の側面にゲートを設けることが可能なため、完成したゲート跡が目立たない製品を作ることができます。
ピンゲート同様、型開き時にゲートが自動的にカットされるため、後処理の手間も減少します。
ダイレクトゲート
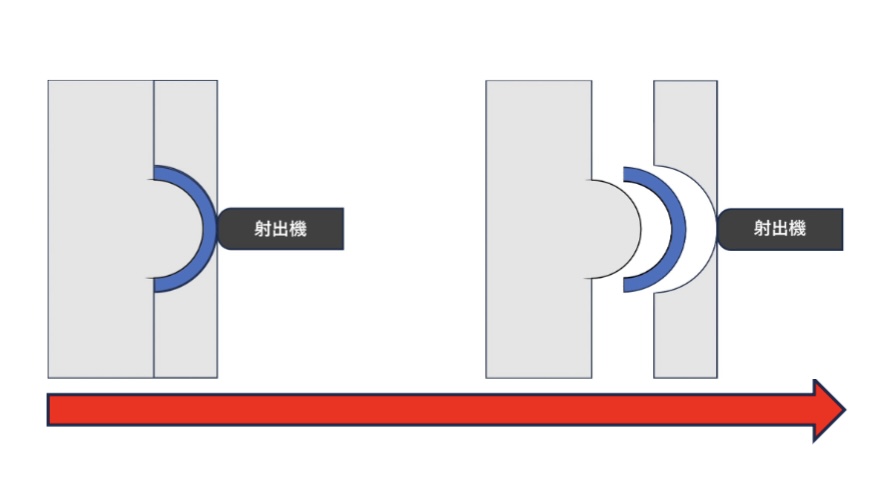
ダイレクトゲートは、スプルーやランナーを通らずに、成形機のノズルから直接金型のキャビティに樹脂を射出するゲート方式です。
スプルーやランナーがなく、ノズルからキャビティまでの流路が短いため、流れる樹脂の量を減らすことができます。また、ゲート部の断面積が大きいため、充填圧力が低くて済むという利点もあります。
一方、ゲート跡が大きく目立つため、見た目が重要な部品には不向きであるというデメリットもあります。
各ゲートの長所・短所 比較表
種類 | 長所 | 短所 |
---|---|---|
サイド | ①金型構造が単純でコストが低い ②複数個取りに対応可能 ③意匠面を避けた箇所(製品の側面)にゲート跡を残せる ④ゲート口が比較的大きく、樹脂の流れがスムーズ(圧力損失が少ない) | ①後工程でゲートカットが必要 ②ゲート跡が比較的大きく、目立つ |
ピン | ①複数個取りに対応可能 ②ゲートが小さいため、小型部品も生産可能 ③ゲートを複数設置できるため、面が広い製品や形状が複雑な製品も高品質で生産可能 ④3プレート構造のため型開き時に自動でゲートカットされる ⑤ゲート跡が小さく、目立ちにくい | ①金型構造が複雑でコストが高い ②意匠面(製品の正面)にゲート跡が残る ③ランナーが長いため、材料の使用量が多い ④ゲート口が小さく、樹脂の流れが悪い(圧力損失が大きい |
トンネル | ①型開き時に自動でゲートカットされる ②意匠面を避けた箇所(製品の側面)にゲート跡を残せる ③ゲート跡が小さく、目立たない | ①金型構造が複雑でコストが高い ②複数個取りに対応しにくい ③ゲート口が小さく、樹脂の流れが悪い(圧力損失が大きい) |
ダイレクト | ①ランナーがないため、材料の使用量が少ない ②ゲート口が大きく、樹脂の流れがスムーズ(圧力損失が少ない) | ①一個取りにしか対応できない ②後工程でゲートカットが必要 ③ゲート跡が大きく、目立つ |
おわりに
本記事では、射出成形のゲートの種類とそれぞれの特徴をご説明しました。
ゲートの選択は製品の品質と生産効率に大きく影響を与えるため、設計段階での正しい選択が不可欠です。
各ゲートタイプの利点と制約を理解し、それを自身のプロジェクトや製品設計に活かしていただければと思います。